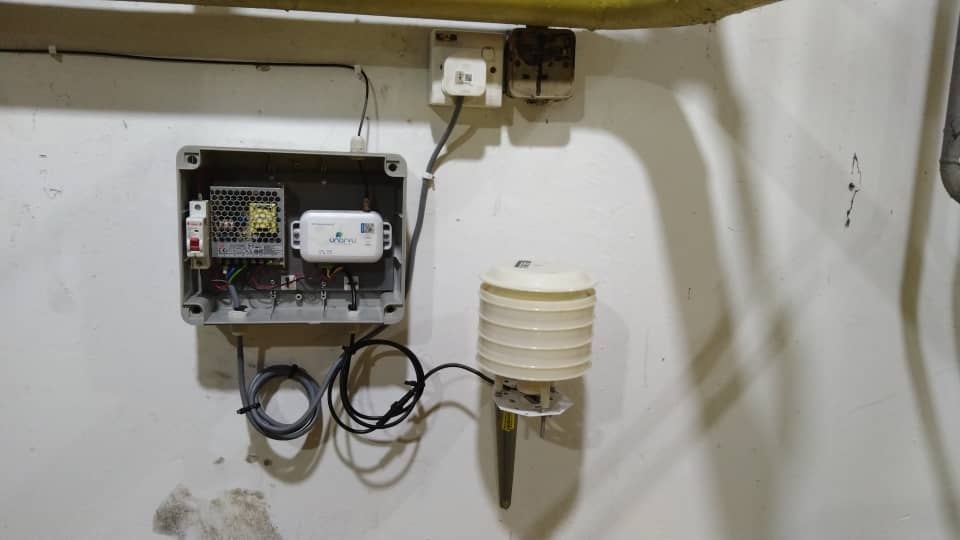
Ensuring Worker Safety with Favoriot’s Advanced Ammonia Monitoring in Poultry Processing
September 2nd, 2023 Posted by favoriotadmin BLOG 0 thoughts on “Ensuring Worker Safety with Favoriot’s Advanced Ammonia Monitoring in Poultry Processing”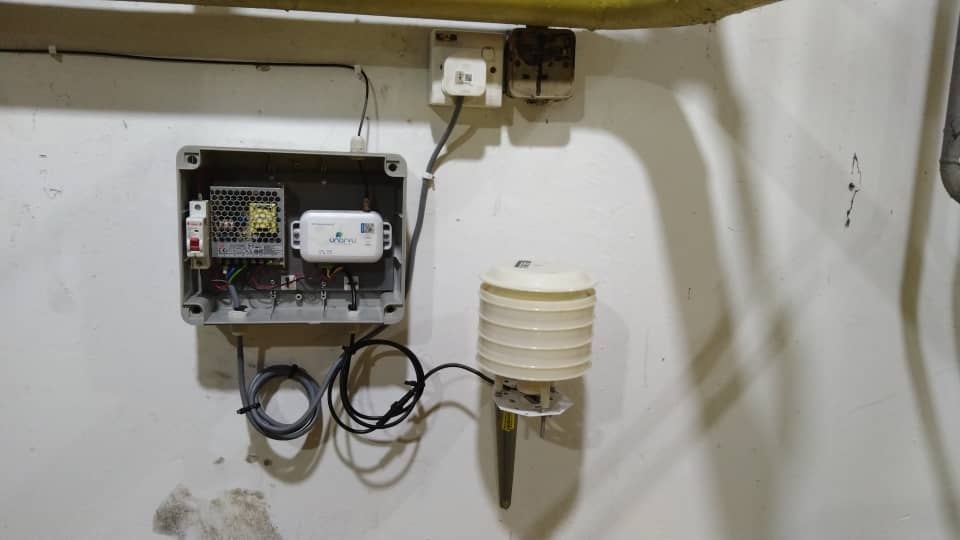
Introduction: The Complexity of Safety and Efficiency in Poultry Processing
Managing a poultry processing plant involves more than just efficient production. It is a complex endeavor that demands a keen focus on both efficiency and worker safety, particularly when ammonia is used for refrigeration. This chemical serves as an effective coolant but comes with its own set of hazardous properties that, if not managed correctly, can pose significant health risks. Favoriot’s innovative gas monitoring technology offers a comprehensive solution for maintaining a safe working environment.
The Role of Ammonia: An Essential yet Hazardous Component
Ammonia is indispensable for rapid cooling in poultry processing, thus minimizing the risk of bacterial contamination. However, its utility comes at a price. Overexposure to ammonia can result in respiratory issues, eye irritation, and, in severe cases, life-threatening conditions.
Traditional Methods: The Limitations of Manual Monitoring
Previously, monitoring ammonia levels was an arduous task that required personnel to engage in direct, manual measurement. This approach not only opened the door for human error but also increased the risk of exposure to hazardous concentrations of ammonia.
The Favoriot Solution: State-of-the-Art Ammonia Monitoring
Favoriot has engineered a cutting-edge smart gas monitoring system tailored for ammonia detection. Utilizing a combination of advanced sensors and Internet of Things (IoT) technology, this system offers a host of features designed to enhance safety.
Key Features:
- Continuous Monitoring: The system operates around the clock, providing real-time data and effectively reducing the risks associated with periodic manual checks.
- Remote Access: It allows supervisors and safety personnel to monitor ammonia levels from remote locations, eliminating the need to enter high-risk areas.
- Automated Alerts: The system is configured to send immediate notifications via email or SMS if ammonia levels exceed predetermined safety thresholds.
- Data Logging: Comprehensive data records are maintained, facilitating trend analysis and future safety measures.
The Impact: Favoriot as a Crucial Safety Measure
The real-time monitoring provided by Favoriot serves as an early warning system. Immediate interventions can be initiated, whether that involves venting the gas, adjusting operational parameters, or evacuating personnel. Consequently, this not only protects lives in emergency situations but also contributes to the general well-being of workers on a day-to-day basis.
Conclusion: The Imperative of Adopting Advanced Safety Measures
For those in the poultry processing industry, integrating Favoriot’s smart gas monitoring system into your safety protocols is highly advisable. The technology not only secures a safer working environment but also protects your most valuable asset—your workforce.
In summary, Favoriot’s system offers a seamless blend of technology and safety, setting a new standard in poultry processing. Safety should always be the first priority, thereby ensuring both product quality and workforce well-being.